Oxygen Sensor Training Guide
Download Printable PDF Training Guide
3.0 OXYGEN SENSOR TYPES & FUNCTION
Unheated
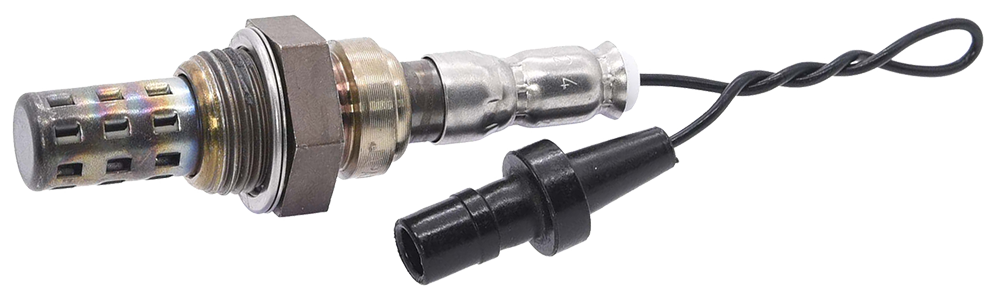
A one wire or two wire unheated oxygen sensor is the earliest and most basic type of sensor. One wire sensors employ only a signal wire, while two wire versions also have a wire going to ground. Unheated sensors require external heat and thus can only be located close to the engine’s exhaust ports, which are not ideal locations in which to measure A/F ratio. Another limitation of the unheated sensor is that it can take a minute or longer to reach the temperature required for proper operation.
Heated
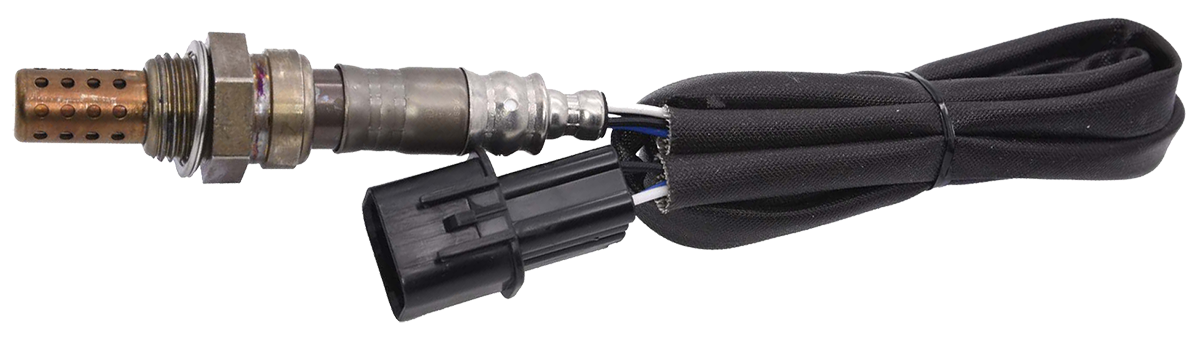
Three and four wire heated oxygen sensors evolved in order to reach operational temperature more rapidly.
The heater element is an internal resistor that heats up as via an electrical current that is passed through it. Heated sensors can be placed in downstream locations on the exhaust system and will stay at the proper temperature for a longer period of time than unheated sensors. All modern oxygen sensors employ a heater, though the type and heat- up times vary.
FLO & UFLO
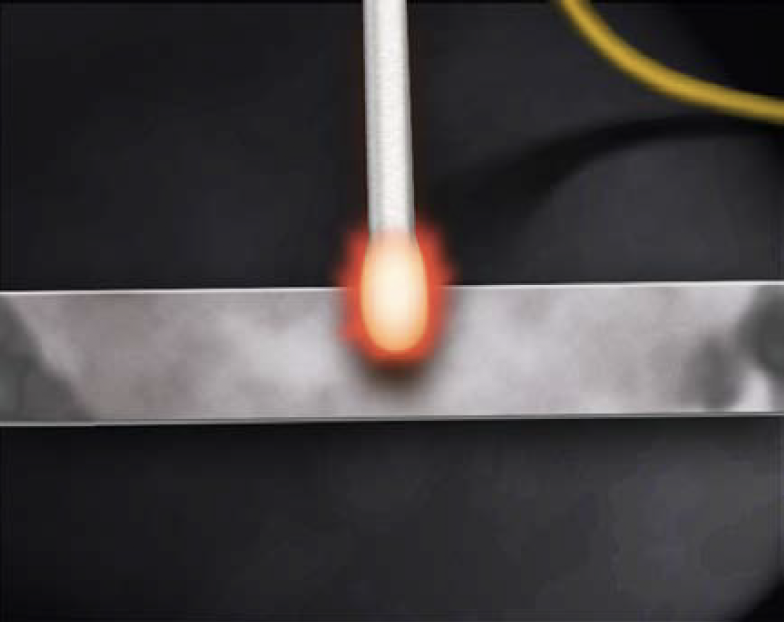
Fast Light Off and Ultra-Fast Light Off sensors employ a low resistance, high watt density heater in order to expedite warm up time. These sensors can reach operating temperature in as little as twenty seconds. Since vehicle emissions are at their most harmful when a vehicle is cold, FLO and UFLO are able to help reduce pollution where other sensors cannot. Exposed heater element shown on left.
Planar
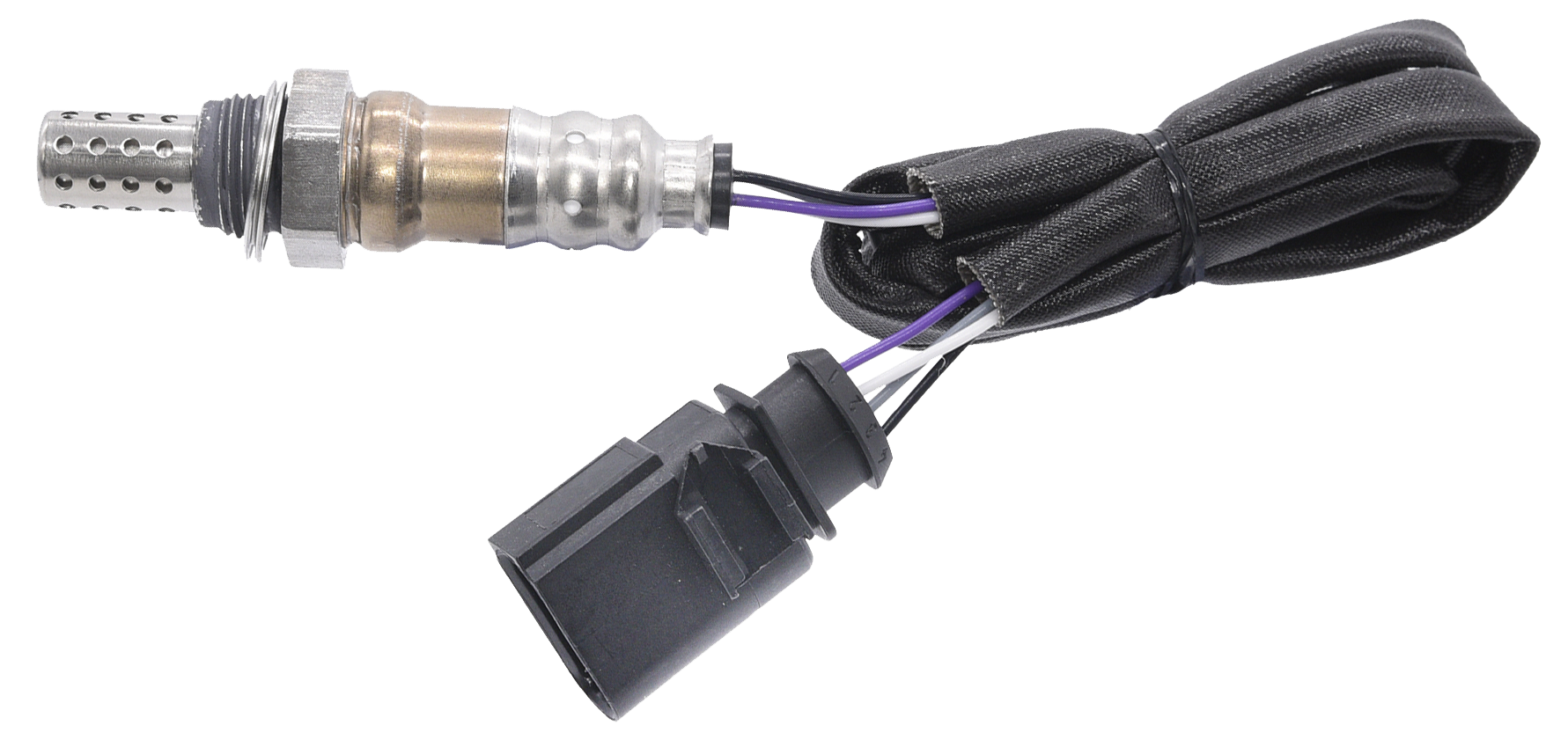
Planar sensors use layers of zirconia and alumina bonded together. This technology allows for much faster warm up of the sensor because there is a much lower mass to heat and the heater is in direct contact with the sensing portion. Typical warm up time for planar sensors ranges from five to thirty seconds.
Air Fuel Ratio and Wideband
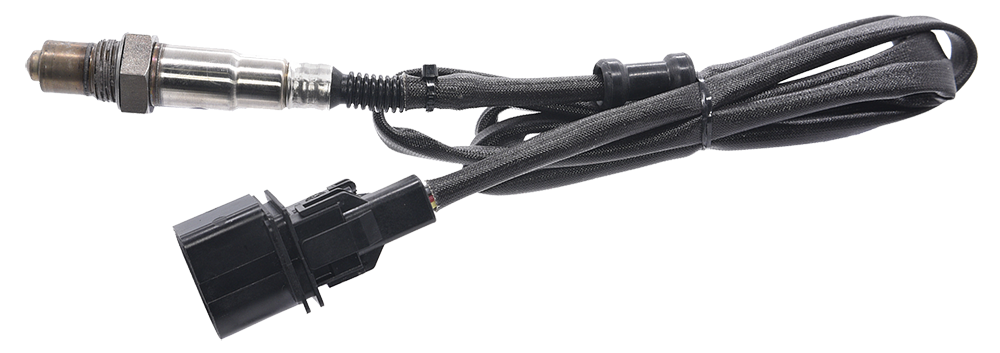
Five wire wideband sensors were introduced in 1994. Along with four wire air fuel ratio sensors, they represent the state of the art in sensor technology. They eliminate the lean-rich cycling inherent in narrow-band sensors, allowing the control unit to adjust the fuel delivery and ignition timing of the engine much more rapidly.
Universal vs. Direct Fit
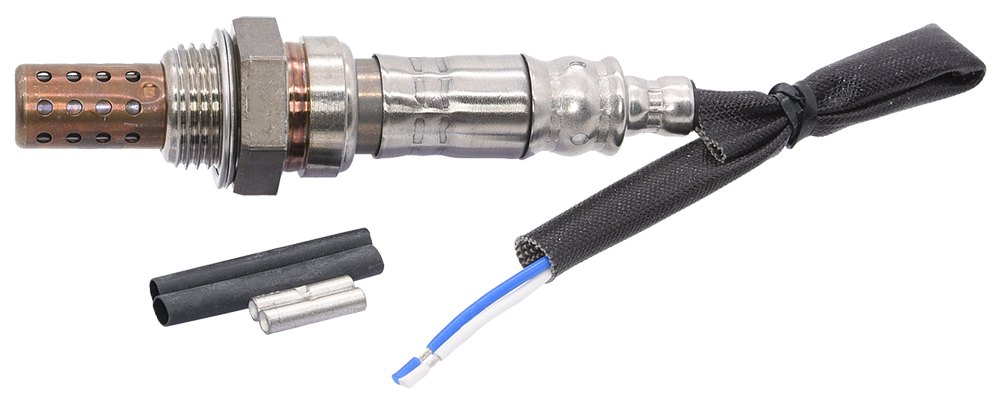
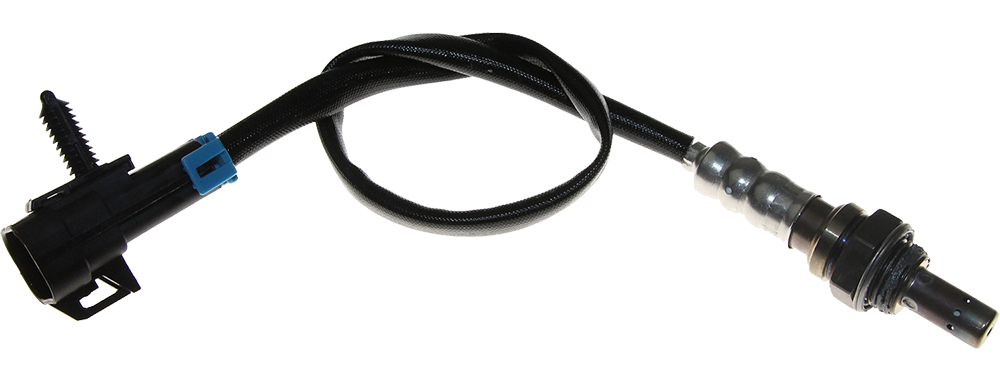
Universal sensors can be made to fit a variety of applications providing that the sensor is the correct type for the vehicle in question. Connections must be made by splicing the correct wires into the corresponding wires on the existing harness. In the U.S. aftermarket, universal sensors are rarely used as the marketplace prefers the fit, form, and function that direct fit sensors provide.
As their name suggests, direct fit sensors are made to fit specific applications via a connector that fits directly into the existing connector on the vehicle. Direct fit connectors are often the preferred choice of installers.
This is because they offer ease of installation over the inherent risks of making multiple splices. The nature of the connecter also helps ensure that the correct replacement part has been chosen.
OE vs. Aftermarket
Original Equipment sensors are the original sensors that were on a vehicle when it left the factory. There are several different providers of OE sensors that are chosen by vehicle manufacturers.
When OE sensors need to be replaced, an Aftermarket sensor can offer matched quality at a reduced cost. Therefore, aftermarket sensors are often the choice of installers and DIY individuals for replacement purposes.